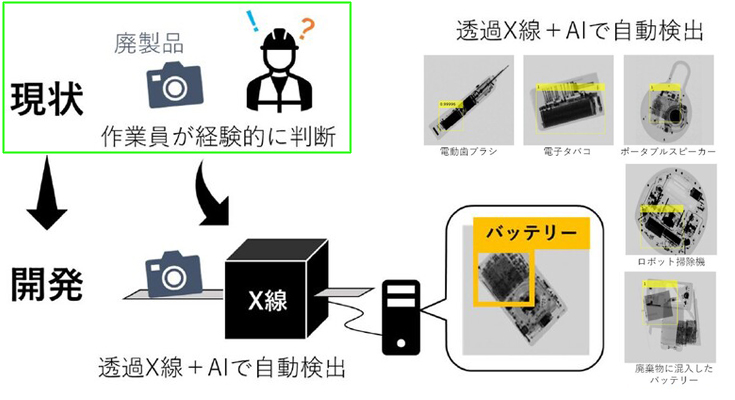
産総研(国立研究開発法人 産業技術総合研究所)は、廃製品・廃棄物の内部を透過X線で透視し、複数のAIによるバッテリー検出プログラムを使って、高精度かつ網羅的にバッテリーを自動検出するシステムを開発したことを発表した。
これにより、リサイクル施設等において、作業員が手作業で実施している廃製品・廃棄物内部のバッテリー有無の判断を自動化でき、処理の速さと精度を向上させ、バッテリー誤破砕による火災発生の防止にもつなげることができる。
この技術は、産総研 エネルギー・環境領域研究企画室 上田 高生 企画主幹と、環境創生研究部門 資源価値創生研究グループ 古屋仲 茂樹 上級主任研究員、環境創生研究部門 大木 達也 首席研究員らが開発した。
【この技術のポイント】
・透過X線およびAI(深層学習ネットワーク)の組み合わせにより実現
・多数のAIがバッテリーの有無を正しく判断して見落とさない
・作業員に代わって検出と選別をシステム化
リサイクル施設で破砕機へバッテリーの誤投入の火災は年間約4500件
全国のリサイクル施設において、廃製品・廃棄物に混入したバッテリーを破砕機へ誤投入することによる火災が多く発生していて、問題のひとつになっている。出火に至る火災が年間約4500件、火花の発生を含めると年間約9000件も発生している。
環境省の報告によれば(※)、これらの約半数が解体・破砕工程で発生していて、このような火災を防止するため、廃製品・廃棄物が破砕機に投入される前に、内蔵または混入したバッテリーを見つけ出す必要がある。現在のリサイクル施設では、廃製品・廃棄物を作業員が手作業で確認、バッテリーの有無を経験的に判断しているという。
この方法では時間と手間がかかり、バッテリーを内蔵する製品の多様性が、有無の判断を困難にしている。
(※環境省「令和2年度リチウムイオン電池等処理困難物適正処理対策検討業務結果」)
透過X線で内蔵バッテリーを認識
産総研は小型デジタル家電を対象とした、自動・自律型リサイクルプラントの開発に取り組むとともに(2023年1月12日、日本経済新聞「スマホの希少金属、高効率回収 産総研などライン自動化」、産総研プレス発表、2018年6月20日、https://www.aist.go.jp/aist_j/news/pr20180620.html)、スマートフォンやタブレット端末を自動解体するにあたり、内蔵されているバッテリーを傷つけないための研究開発をおこなってきた。製品によって内部構造は千差万別なため、非破壊で内部構造を正確に把握する技術が求められた。
そこで、透過X線によりスマートフォンまたはタブレットの内部構造を透視し、その画像をAI(深層学習ネットワーク)で分析してバッテリーを把握する技術を開発した。今回は、その技術を応用し、スマートフォンやタブレットだけでなく、さまざまな品目の廃製品に内蔵されたバッテリーを検出することに成功した。
この研究開発は、国立研究開発法人新エネルギー・産業技術総合開発機構(NEDO)による「高効率な資源循環システムを構築するためのリサイクル技術の研究開発事業(2017~2023)」の支援を受けた。
高精度と網羅性はトレードオフという課題
今回の研究開発では、バッテリーを検出するプログラムにおいて、高精度と網羅性を両立することが課題だったという。一般的にAIによる検出では、画像内のさまざまな領域について対象物(この研究ではバッテリー)が含まれる予測確率(信頼度スコア)を計算。そして、ユーザーがあらかじめ設定した閾値(いきち)より信頼度スコアが高い領域を検出する。従って、閾値により検出結果が変わってくる。すなわち、高い閾値を設定すれば、検出結果が正しい可能性が向上するものの(精度が高い)、バッテリーが検出漏れとなる可能性も上がってしまう(網羅性が低い)。反対に低い閾値を設定すると、信頼度スコアが低い領域まで検出されるため、検出結果にバッテリーでないものも含まれてしまう確率が増加し(精度が低い)、一方でバッテリーの検出漏れは減る(網羅性が高い)。このように、高精度と網羅性はトレードオフの関係にあり、両立は困難だった。しかし、リサイクル施設では、大量の廃製品を迅速かつ安全に処理する必要があるため、高精度と網羅性を両立させた検出プログラムが求められきた。
透過X線とAIによるバッテリー検出という発想は、2021年に論文発表されてたが、高精度と網羅性の両立に課題があり、自動検出できる実用的な技術・システムは開発されていなかったという。
判断が異なる複数のAIを併用
今回開発したバッテリー検出プログラムは、独自に考案した3段階の処理プロセスに特徴がある(図1)。透過X線画像が入力されると(図1(a))、第1段階でAIが画像を分析し、第2段階の処理に適した領域を抽出(図1(b)の青・緑枠)。第2段階は、得意とする画像タイプがそれぞれ異なる10種類以上のAIから構成されており、第1段階で抽出された領域ごとに、最適な専用ネットワークを用いてバッテリーを検出(図1(c))。第3段階は、第2段階よりも精度は低いが高い網羅性を有するAIにより、第2段階で見落とされたバッテリーを検出する(図1(d))。開発したプログラムの処理速度は、1画像あたり約1秒。
深層学習ネットワークの構築には、約3400個のサンプルを複数回ずつ透過X線撮影した画像を使用し、95%を学習用、残り5%を性能評価用として利用した。
開発したプログラムの性能の検証は、150個のサンプルを1回ずつ透過X線撮影した画像によっておこなった。サンプルは、以下に例示する品目などのほか、廃棄物にバッテリーを混入させた物、および単体のバッテリー等から構成。これらは、過去に火災の原因となったと推定されている品目やリサイクル施設で判断に困っている品目を参考に選定した。
バッテリーを自動検出する従来製品は存在しない。そこで、開発したプログラムの性能の評価用に1種類のAIを使った検出プログラムを作成して、比較対象とした。
「開発したプログラム」と「比較プログラム」で、150枚の画像からバッテリー検出を試みた。検出結果の評価として、精度に相当する”Precision”と網羅性に相当する”Recall”という指標を用いた。どちらの指標も0~1の値を取り、値が大きいほど高い性能を示す。
図2に検証結果を示す。まず開発したプログラムと比較プログラム(高い閾値)を比べる(図2①②)。精度は同程度だが、網羅性は比較プログラムがやや劣っている。リサイクル施設におけるバッテリーの検出漏れを防ぐには高い網羅性が求められる。そこで今度は、比較プログラムの閾値を低い値に設定すると、網羅性は高くなった一方で、精度は低くなってしまった(図2③)。このように、比較プログラムでは高精度と網羅性がトレードオフになるのに対して、開発したプログラムでは精度と網羅性を高いレベルで両立できていることが分かった。
図3は開発したプログラムによるバッテリー検出結果の例。
識別プログラムを搭載した自動検出・選別システムを開発
このプログラムを搭載した自動検出・選別システムを開発。図4に示すとおり、透過X線装置(㈱イシダ製X線検査装置)、開発したプログラムを搭載したパソコン(PC)および振分装置をベルトコンベヤーで連接した。廃製品・廃棄物は、投入後に透過X線撮影され、その画像がネットワーク対応ハードディスクドライブ(NAS)に保存される。プログラムが、新たに保存された画像を自動的に解析して、バッテリーの有無を判断。その情報は振分装置に送られて、ベルトコンベヤーの上下動により、廃製品・廃棄物が選別される。このように本開発プログラムは、NASに画像保存する機能を持つ既存の透過X線装置に連接され、自動検出・選別システムの一部として機能する。
振分装置の仕様により、現在のところ1画像あたり6秒の処理速度にしているが、振分装置の改良により開発したプログラムの処理速度を、本来の性能の1秒/画像まで高速化できる見込みだとしている。
この研究開発にあたり、株式会社リーテムおよび大栄環境株式会社から廃製品サンプルの提供を受けた。
今後の予定
今後は、このシステムをリサイクル施設で活用するため、リサイクル企業などの連携先を募集。また、開発したプログラムの活用範囲を広げるため、より大型または高解像度のX線装置との連接、バッテリーの種類の識別、バッテリー以外の対象物の検出などの課題に取り組んでいく考えだ。
Precision
深層学習などによる検出結果の評価に用いられ、検出結果に正しく検出対象物が含まれている程度を表す指標。深層学習プログラムにより検出された画像内の領域と実際に検出対象物がある領域を比較して計測される、真陽性(TP:正しい検出)および偽陽性(FP:誤検出)の数から、Precision = TP / (TP + FP)で計算される。「適合率」とも呼ばれる。
Recall
深層学習などによる検出結果の評価に用いられ、検出対象物の検出漏れの少なさを表す指標。TPおよび偽陰性(FN:検出漏れ)の数から、Recall = TP / (TP + FN)で計算される。「再現率」とも呼ばれる。
この記事を読んだ人におすすめ
関連する記事はまだありません