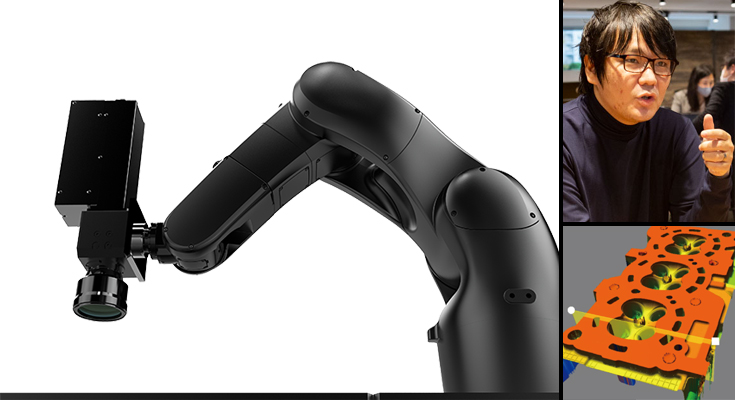
2005年にノーベル物理学賞を受賞した「光コム」という技術を社会に活かしている企業が日本にある。「光コム」技術を3次元の形状測定分野で実用化した「XTIA」(クティア)だ。
JUKIやニコンなどの大手企業とのアライアンスも進め、エンジンのシリンダー内部を高精度に計測するなど、生産工場の現場などで導入されている。来年にはロボットアームと組み合わせたソリューションもリリースする予定だ。
この注目の「光コム」、そのしくみや特徴などを取材し、八木社長にも話を聞いた。
くし状に並んだ光を活用する技術
株式会社XTIAは、2020年2月に技術名からとった社名「株式会社光コム」から名称変更した。海外展開などを視野に入れてのことだ。その際に社長も八木貴郎氏に変わった。
光コムの「コム」はコミュニケーションでもカンパニーでもなく「櫛(くし)」を意味する「Comb」。原理をごくごく簡単に言うと、櫛状に平行して多数の光を発し、その反射光を計測等に活用する技術。生産現場で使えば、高精度で高速な計測が実現できる。「世界で最も精度の高いものさし」の原理と評されているという。
周波数スペクトルは「くし」が並んでいるように見える光源となるのが特徴で、同社は「1500nm付近のレーザを用いて、クラス1の安全なレーザとして取り扱うことができる」としている。
入射光と反射光が同軸の「光コム」技術
光を使った3次元計測技術は実は既にお馴染みだ。しかし、主に用いられているのは「三角測量方式」で「光コム方式」(同軸計測)とは異なる。光はご存じのように直進性が高いがゆえに回り込むことが苦手で、斜めに光が入ったり、それによって影になる部分には光が届かず三角計測ができなかったり計測の精度が低下したりする点が課題だ。
一方、「光コム」は入射光と反射光を同じ軸で、さらには櫛状に複数の同軸光をあてて計測する。この技術を産業用に応用できているのは、XTIAだけだとしている。
また、1秒間に50万点を測定できる高速技術を開発し、下図のような複雑な形状も光で非接触の計測が可能となった。例えば、エンジンのシリンダーヘッドやブロック、タービンなど曲がりくねった形状の部品も高精度でかつ高速に、全数計測することもできるという。特に傷やバリなど、わずかな凹凸の検知も得意だ。
「光コム」技術を使ったシリンダーの計測デモ
百聞は一見にしかず。実用化された光コム技術をデモで見せてもらった。
■ 動画
動画カメラには映っていないが、目視ではレーザー光が赤色でスキャンしている様子がわかる。
光コム技術をロボットアームに搭載
高精細センサー(40x40mmエリアスキャン)をロボットアームと組み合わせることで、あらゆる箇所を気軽にマイクロ精度で測定可能にした。
元々は、ロボットアームは揺らぎをもっているため、それが測定精度に大きく影響をおよぼすことから、高精細な精度の測定は不向きとされていた。しかし、XTIAはロボットアームの揺らぎを制御することにて、マイクロオーダーの精度を確保したという。
このソリューションは来年のリリースに向けて準備を進めている。八木社長は「これによって、新しい次元の検査と測定を実現していきます。多品種測定やあらゆる形状の測定に対応していくための”幅”が大きく向上できると期待されています」と語る。
八木社長インタビュー「光コム技術は生産現場の非接触計測を加速する」
八木社長に更に詳しい話を聞いた。
編集部
光コムの簡単なしくみと、この技術を活用している経緯について教えてください
八木氏
通常の光を使った計測は、ひとつの周波数の1本の光を斜めから照射して真上から撮像する三角測量方式が主流です。それに対して「光コム」技術は1本のレーザーに数10本の周波数の光が等間隔に並んで発射します。光の方向も、1本のレーザーを真上から下に真っ直ぐ発射して真っ直ぐ戻す同軸方式です。「世界で最も精度の高いものさし」の原理と言われています。
この概念自体は1993年に初めて論文で発表されました。発表したのが当社の創業者の興梠(こおろぎ)です(現 取締役名誉フェロー 興梠元伸氏(工学博士))。その後に米国とドイツの学者の方がこの技術が応用物理の中で優れていることを証明し、2005年にノーベル物理学賞を受賞しました。
一方の興梠はこの技術を社会実装するために、この会社を2002年に設立しました。光コムがノーベル賞を受賞するより前のことです。
編集部
なるほど、それでXTIAが光コム技術で最先端の実用化を取り組むことになったのですね。では、光コム技術はどうして製造現場等に優れていると言えるのでしょうか。
八木氏
光コム技術はミクロンの精度を達成するとともに、斜めから光を当てる三角測量方式では計測できない部分の測量にも対応できます。従来の技術では単純な形状のものしか計測できないので、実は製造工場の計測や検品の自動化は思うようには進んでいません。製造現場における自動化は20%程度しか実現できていないと言われていますが、複雑な形状の部品に今までの光技術では対応できなかったことも、自動化が進まない要因のひとつになっていると考えています。
編集部
製造現場の検品などでは、画像認識とディープラーニングなどの技術を組み合わせたものが自動化に活用されはじめていますが、それより優れているのでしょうか。
八木氏
画像認識にも優れた点はあります。例えば、検品時のシミや変色など平面的な不具合の検知です。しかし、傷や打痕、バリなどの凹凸は目視しづらいので光コムの方が優れています。例えば現場では「5ミクロンのバリまでならOKだけど、10ミクロンならNG」といった判断も要求されるケースもあります。更には「エンジンのシリンダー内部(ボア)の”容積”が知りたい」といったものもありますが、それらは画像認識技術では正確な数値はでません。当社では光コムと画像認識を組み合わせ、それぞれのメリットを活かした検品や確認ができるソリューションを来年のリリースに向けて開発しています。
編集部
ロボットアームと組み合わせた検査機も開発中とのことですね
八木氏
検査や検品業務の自動化を更に進めるには、穴の奥や裏側も簡単に検査できるようにすることが重要です。あらゆる角度から高精度な光コム技術で検査できるようにするために、ロボットアームと組み合わせたソリューションを開発中です。
今まで見えなかったところが正確に見えたり、計測できるようになることで、生産現場の自動化は加速すると考えています。
現在、同社はJUKIやニコン、双日などの大手企業とのアライアンス提携し、自動車のエンジン部品などの検査工程に使う検査機器などを開発し、導入を進めている。今後は更に他の検査機器メーカーと連携して技術提供したり、集積したデータ等の販売など、事業の拡大を積極的に行っていく考えだ。
株式会社XTIA 公式ホームページ
この記事を読んだ人におすすめ
関連する記事はまだありません
ABOUT THE AUTHOR /
神崎 洋治
神崎洋治(こうざきようじ) TRISEC International,Inc.代表 「Pepperの衝撃! パーソナルロボットが変える社会とビジネス」(日経BP社)や「人工知能がよ~くわかる本」(秀和システム)の著者。 デジタルカメラ、ロボット、AI、インターネット、セキュリティなどに詳しいテクニカルライター兼コンサルタント。教員免許所有。PC周辺機器メーカーで商品企画、広告、販促、イベント等の責任者を担当。インターネット黎明期に独立してシリコンバレーに渡米。アスキー特派員として海外のベンチャー企業や新製品、各種イベントを取材。日経パソコンや日経ベストPC、月刊アスキー等で連載を執筆したほか、新聞等にも数多く寄稿。IT関連の著書多数(アマゾンの著者ページ)。